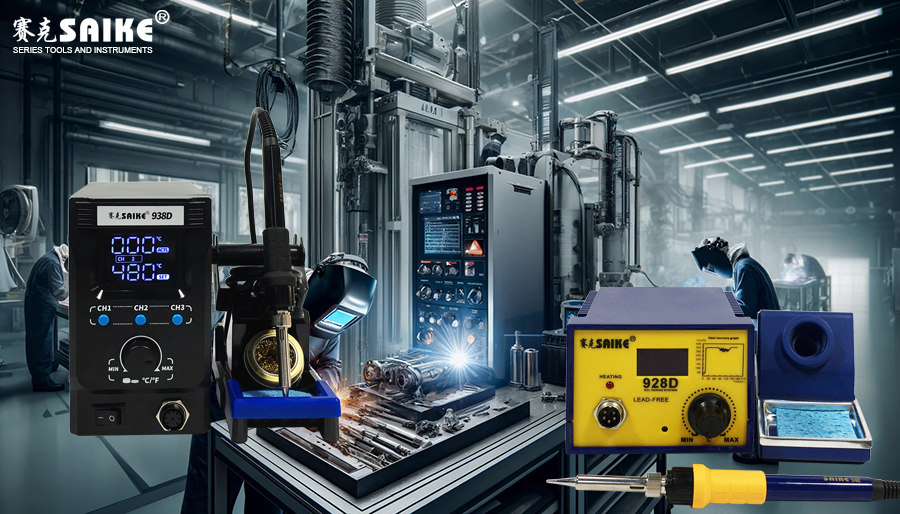
Welding high-temperature alloys and dissimilar metals is a technically challenging activity, especially when performing precision welding on a welding bench. These materials are widely used in aerospace, automotive, energy, chemical, and other industries, where material performance requirements are extremely demanding. High-temperature alloys are characterized by their high-temperature resistance, corrosion resistance, and mechanical strength. Dissimilar metal welding involves joining different metals or alloys that may have significant differences in thermal expansion coefficients, melting points, and electrochemical properties. This article explores the welding technology of high-temperature alloys and dissimilar metals on a welding bench, including material characteristics, welding methods, challenges, and strategies to address them.
I. Welding characteristics of high-temperature alloys
High-temperature alloys, such as nickel-based alloys, titanium alloys, and stainless steel, are widely used in manufacturing components for aero-engines and gas turbines due to their excellent mechanical properties and stability in extreme environments. When welding these materials, the following points need to be noted:
- High-temperature strength: Significant microscopic structural changes may occur in the heat-affected zone during the welding process of high-temperature alloys, potentially affecting the mechanical strength of the weld area.
- Heat crack sensitivity: Many high-temperature alloys are prone to heat cracks during the welding process, especially during rapid cooling.
- Oxidation and corrosion: These materials are susceptible to oxidation at high temperatures. Therefore, welding should be performed in an inert or reducing atmosphere, or special fluxes should be used to protect the weld.
II. Welding characteristics of dissimilar metals
Welding dissimilar metals involves joining two or more metals or alloys with different properties. Challenges of this type of welding include:
- Differences in thermal expansion coefficients: Variations in thermal expansion coefficients between different metals can cause stress in welded joints during the cooling process, leading to deformation or cracking.
- Differences in electrochemical properties: Potential differences between metals can result in electrochemical corrosion in the weld area.
- Differences in melting points: Variations in melting points require precise temperature control during welding to ensure good welding results for both materials.
III. Welding methods and techniques
- Adopting appropriate welding methods: Precision welding techniques such as TIG (Tungsten Inert Gas) or MIG (Metal Inert Gas) welding provide stable heat input and good atmosphere control.
- Using interlayer materials: In dissimilar metal welding, interlayer materials (such as filler metals or intermediate layers) can reduce material property differences and minimize the risk of cracking.
- Precise temperature control: The temperature control function of the welding bench allows precise adjustment of welding temperatures to accommodate different melting points and heat treatment requirements of various metals.
IV. Challenges and strategies
- Preheating and post-heat treatment: Proper preheating and post-heat treatment of welded parts can reduce welding stress and the risk of heat cracks.
- Optimizing welding parameters: Optimize welding speed, energy input, and shielding gas flow rate through experimentation and simulation.
- Welding environment control: Perform welding in a dust-free environment or a specific atmosphere to reduce oxidation and contamination.
V. Conclusion
Welding high-temperature alloys and dissimilar metals on a welding bench is a technically demanding task that requires precise material selection, welding parameters, and environmental control. By adopting advanced welding techniques, refined operational processes, and strict quality control measures, various challenges during the welding process can be effectively addressed. This ensures welding quality and meets the high standards demanded by industries such as aerospace, automotive manufacturing, and energy.