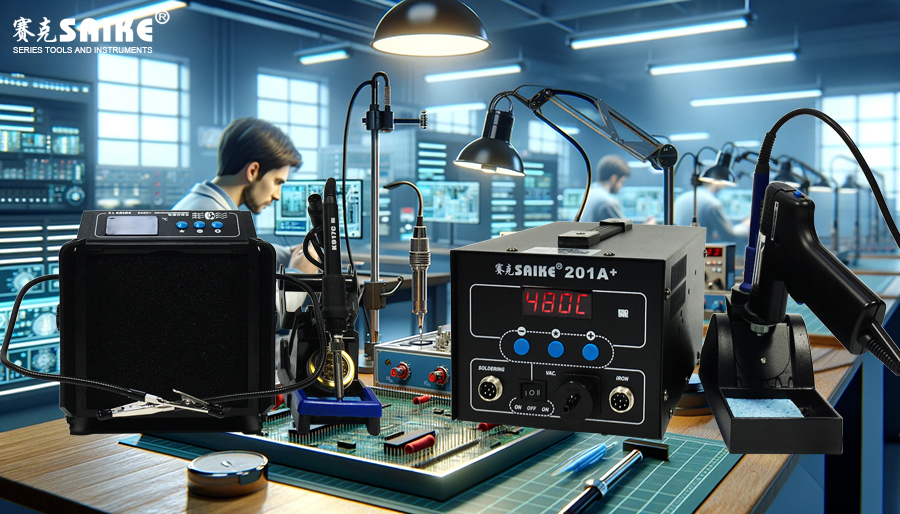
The welding strength of soldering stations is one of the key indicators for evaluating welding quality, which directly affects the reliability and durability of electronic components during use. Therefore, rigorous testing of welding strength is crucial. This article will explore several commonly used welding strength testing methods to ensure that the welding process meets the product’s performance requirements.
I. The Importance of Welding Strength Testing
Welding strength testing is used to assess whether solder joints can withstand the mechanical and thermal stresses that may be encountered in practical applications. Good welding strength means that the solder joints can maintain stable electrical and mechanical connections throughout the product’s lifespan, avoiding failures caused by solder joint breakage or detachment.
II. Welding Strength Testing Methods
- Pull Test
The pull test is a direct method to evaluate the mechanical strength of welded connections. It assesses the strength of the solder joints by measuring the force required to break them.
- Shear Test
The shear test measures the ability of a solder joint to resist shear forces, typically applied parallel to the welded parts.
- Fatigue Test
The fatigue test assesses the durability of solder joints under repeated stress, which is especially important for mobile devices or electronic equipment used in vibrating environments.
- Thermal Cycling Test
The thermal cycling test simulates the performance of solder joints in a changing temperature environment, ensuring good connectivity under thermal expansion and contraction.
III. Conclusion
Through the above welding strength testing methods, the welding quality can be comprehensively evaluated, and it can be ensured that the welding points meet the product’s reliability requirements. Establishing strict testing standards and procedures plays a vital role in improving product quality and reducing failure rates. Regular welding quality inspections and strength tests are key links to ensure the stability of the manufacturing process and product consistency. Correct implementation of these tests can help manufacturers optimize the welding process and enhance the market competitiveness of the final product.