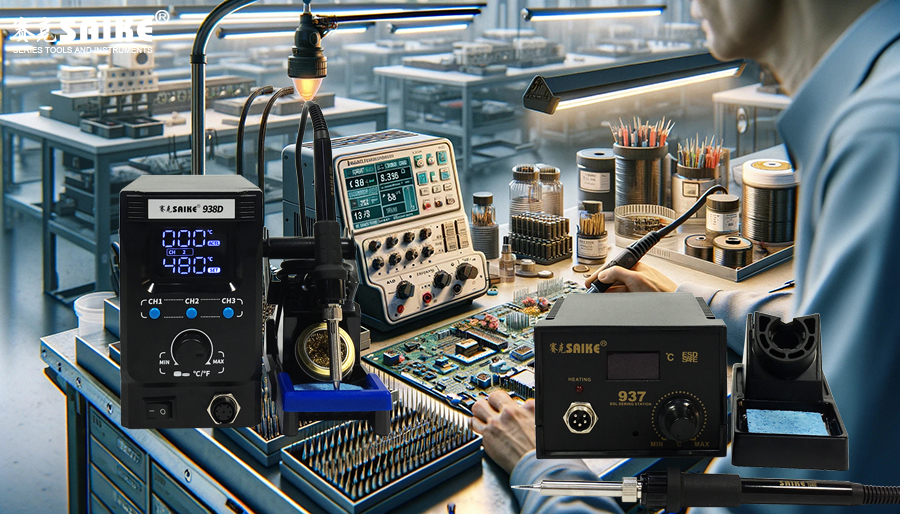
In the field of electronic manufacturing and maintenance, the correct selection and adjustment of soldering station welding process parameters are crucial to ensuring high-quality welding results. The parameters of the soldering station welding process include temperature setting, soldering tip selection, solder type, and soldering speed. This article will explore the selection and adjustment methods of these parameters in detail, helping operators optimize the welding process and improve welding efficiency and connection quality.
I. Temperature Setting
The temperature setting of the soldering station is one of the most important parameters affecting the welding quality. The choice of temperature depends on the type of solder used, the thermal sensitivity of the welded material, and the size of the welding target.
- Solder type: Different solders have different melting points. For example, the melting point of common tin-lead solder is about 183°C to 190°C, while the melting point of lead-free solder is usually above 217°C. The temperature of the soldering station needs to be set above the melting point of the solder to ensure that the solder can fully melt.
- Material thermal sensitivity: Sensitive electronic components (such as semiconductor devices) may not withstand excessive temperatures, so it is recommended to use lower welding temperatures and more precise temperature control systems.
- Recommended temperature range: For most electronic welding work, it is appropriate to set the soldering station temperature between 250°C and 350°C. The specific temperature should be fine-tuned according to the actual situation.
II. Selection of Soldering Tip
The shape and size of the soldering tip directly affect heat transfer and solder joint accuracy. Choosing the right soldering tip can improve welding efficiency and reduce problems of overheating or insufficient heating.
- Pointed tip: Suitable for precise welding tasks, such as welding small SMD components or reaching difficult-to-access solder joints.
- Beveled or knife-shaped tip: Suitable for drag soldering or welding multi-pin components, which can heat multiple pins simultaneously.
- Large flat tip: Suitable for large solder joints, which can quickly heat a larger welding area.
III. Selection of Solder
The choice of solder not only affects the setting of the welding temperature but also relates to the mechanical strength and electrical performance of the welded connection.
- Tin-lead solder: Easy to use, low melting point, suitable for beginners and applications that do not require lead-free.
- Lead-free solder: Environmentally friendly, ROHS compliant, suitable for professional electronic product manufacturing. Usually requires a higher welding temperature.
IV. Welding Speed
The welding speed needs to be adjusted according to the complexity and precision of the welding task. Too fast a speed may lead to cold soldering or uneven solder distribution, while too slow a speed may cause thermal damage.
- Fast welding: Suitable for simple or large-area soldering points, which can improve production efficiency.
- Slow and precise welding: Suitable for complex or precise welding tasks to ensure welding quality.
Conclusion
The correct selection and adjustment of the soldering station welding process parameters are the keys to achieving efficient and high-quality welding. Operators should comprehensively consider the characteristics of welding materials, components, and the welding environment, continuously test and optimize parameter settings to achieve the best welding effect. Accumulating experience through continuous practice and making appropriate adjustments to different situations is an important way to improve welding skills.