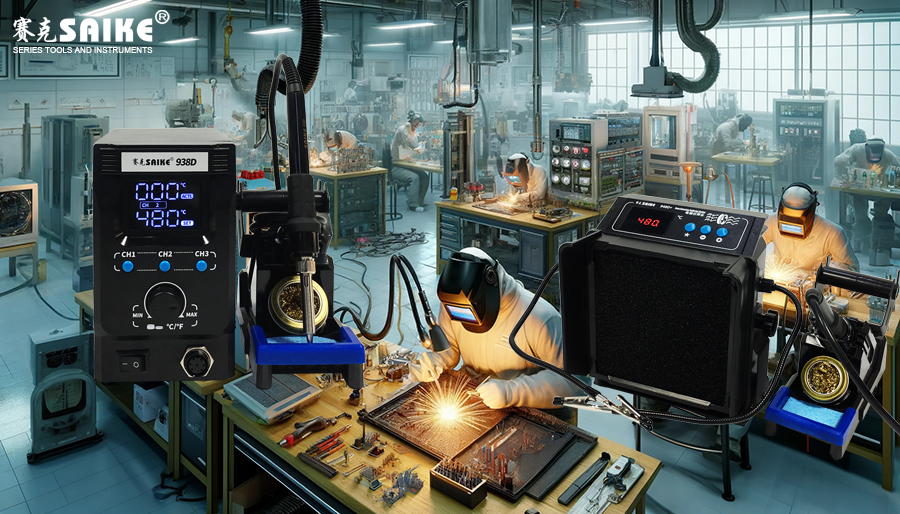
I. Welding Definition
Welding is a process that joins metals or other thermoplastic materials by melting and fusing them. In welding, two or more workpieces are atomically bonded together to form a permanent joint, usually with the help of a filler material (such as solder). This process involves heating, pressure, or a combination of both. Welding is not only used to join metals but also certain non-metallic materials like plastics.
A welding station, one of the primary tools for welding, provides a stable and controllable welding environment. Typically consisting of a soldering iron holder, a control console, and a soldering iron (handle), it enables precise control over temperature and time, ensuring welding quality and efficiency.
II. Welding Classification
Based on welding methods, equipment, and materials, welding can be classified into various types. Here are some major categories:
- Arc Welding: Uses an electric arc as the heat source to melt the metal and welding rod, forming a molten metal pool in the joint gap. It solidifies upon cooling, creating a welded joint. Arc welding is one of the most commonly used welding methods.
- Gas Welding: Utilizes a flame generated by burning a mixture of combustible and oxidizer gases as the heat source. It melts the welding parts and filler metal to form a welded joint. Gas welding is mainly applied to thin steel plates, low-melting-point metals, and brazing.
- Laser Welding: Employs a focused laser beam as the energy source to bombard the welding parts, generating heat for welding. Laser welding offers deep penetration, high speed, minimal deformation, and good stability.
- Resistance Welding: Uses the resistance heat generated when current passes through the welding parts and contacts as the heat source. It locally melts the welding parts while applying pressure for welding. Resistance welding includes spot welding, seam welding, projection welding, and butt welding.
- High-Frequency Welding: Leverages the skin effect and proximity effect of high-frequency current to locally heat the workpiece at the welding site. It then rapidly cools and solidifies to form a welded joint. High-frequency welding is primarily used for welding the longitudinal or spiral seams of pipe fittings.
In addition to the above classifications, there are special welding methods like electron beam welding and ultrasonic welding, each with unique characteristics suitable for different application scenarios.
III. Welding Classification in Welding Stations
Welding methods can be classified based on heat source, pressurization method, protection method, etc. The following are some major welding categories, each potentially used in welding station operations:
- Fusion Welding
- Pressure Welding
In the context of welding stations, welding can also be categorized based on the welding method and requirements:
- Manual Welding: The operator holds the soldering iron for welding. This method is flexible but requires high operational skill and experience.
- Semi-Automatic Welding: The welding station is equipped with some automation devices, but operator involvement is still necessary. This method combines the advantages of manual and automatic welding, improving efficiency and quality.
- Fully Automatic Welding: The entire welding process is automated, requiring no human intervention. It is suitable for mass production, offering high efficiency and stable quality.
IV. Application of Welding Stations in Welding
Welding stations are primarily used for soldering and brazing in electronic manufacturing and maintenance. They provide necessary temperature control and a stable operating platform for welding. Modern welding stations often come with the following features to support complex welding tasks:
- Precise temperature control: Allows users to select the appropriate temperature based on different solders and components.
- Integrated smoke extractor: It sucks away harmful fumes during the welding process to protect the operator’s health.
- Multifunctional head: Equipped with soldering iron tips of different shapes and sizes to adapt to different welding needs.
- Auxiliary tools: Such as solder suckers, hot air guns, etc., to enhance welding efficiency and quality.
Conclusion
It is crucial for professionals engaged in related work to understand the basic classification of welding and the application of welding stations in various welding types. Whether in product design, assembly lines, or maintenance work, selecting the correct welding technology and equipment is the key to ensuring structural integrity and functional reliability.